不良率を見逃すな!システムで品質と効率を向上させる方法
3月も終盤に差し掛かり、新年度が間近に迫っています。このタイミングで、 製品不良への対応について再考してみてはいかがでしょうか。
人の手が加わる限り、 不良品の発生は避けられませんが、重要なのはその内容を分析し、継続的な改善に活かすことです。
今回は、システムを活用して効率的かつ確実に品質管理レベルを向上させる方法をご紹介します。
なぜ不良率や歩留まり率に注目すべきか?
不良率や歩留まり率の管理は、得意先様の信頼獲得と自社のコスト削減に直結します。
例えば、加工会社AとBの2社が候補に挙がっているとします。
A社は良品率95%でコストは相場よりやや高め、
B社は良品率80%でコストは平均的、
とします。あなたが発注先を選ぶ立場であれば、どちらを選択しますか??
やはり値段が安いほうが魅力に感じますか?
コスパ優先で、B社を選択した場合に考えられるリスク
B社を選択した場合、以下のようなリスクが考えられます
1,納期遅延:不良品の再加工や交換に時間がかかり、納期に遅れが生じる可能性があります。
2,顧客への影響:納期遅延や品質問題により、最終的に顧客に迷惑をかけることになります。
3,取引関係の悪化:品質問題が続くと、取引先からの信頼を失い、最終的には取引中止となるリスクがあります。
これらのことから、価格面でB社を選ぶのは将来的なデメリットがあります。 一方で、A社における「良品率」の高さを評価して発注先に選んだ場合、自社におけるお取引先に対しての信頼獲得だけでなく、在庫や材料費用の削減といった経済的メリットももたらします。
システムによる品質管理の効率化
では、現在の作業効率を維持しつつ、どのように品質管理を行うべきでしょうか?
それには、生産管理システムの導入が効果的です。
弊社のi-PROWは、トラブル管理機能を備えており、簡単な操作でトラブルの登録・集計が可能です。
これにより、ペーパーレス化が促進され、災害リスクへの対応も強化されます。
i-PROW(アイプロダブル)~ 実際の操作性のご紹介 ~
日々の業務の中で起きたトラブルに対し、つい忙しさとそして慣れたやり方であることから、「手書き記録の方が早い」と感じられる方もいらっしゃるかもしれません。
そこで、ほんの一部ではありますが、i-PROWの操作手順をご紹介します。
工程実績入力の場面から一瞬でトラブル管理画面に遷移ができ、不適合内容や原因の登録完了までの流れが、以下の動画でご覧いただけます。
この一連の手順で、基礎的なデータを簡単に記録できます。
トラブルの見える化も簡単!
i-PROWの見える化機能の中には、以下のように「トラブル関係」をグラフ化して可視化できる機能もあります。
どんな不適合内容が多いのか、またその原因は何だったのか、そしてどの製品に不良発生が多いのか、どの工程でトラブル発生率が高いのか、などが一目瞭然です。
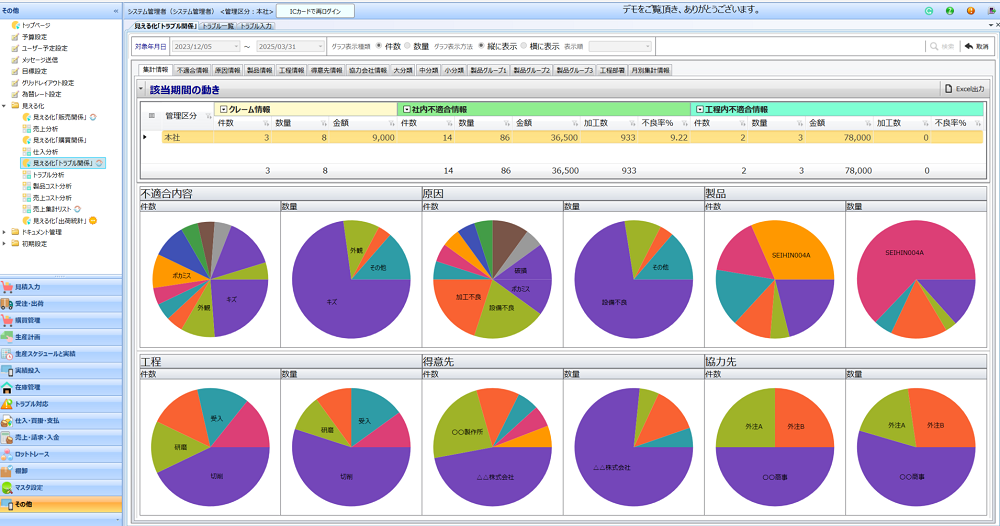
i-PROWの見える化機能「トラブル関係」
トラブル入力のデータを蓄積していくことで、ワンクリックで集計が可能となりますので、工場管理の課題がひと目で分かる上に、月末や年度末の資料作成の負担が軽減されます。
品質管理はぜひi-PROWにお任せください。システムを活用することで、品質向上と業務効率化を同時に実現できます。
雑誌「工場管理」5月号に広告出稿します
製造業においてトラブル管理は「工場管理」にも直結する、というお話をさせていただいたところでご紹介ですが、日刊工業新聞社様発刊の「工場管理」という雑誌はご存知ですか?
「工場管理2025年5月号」では、「異物不良ゼロへの経験則体系~原則を学び整備すれば異物不良はなくせる~」というテーマが特集されるそうです。
(参考URL:日刊工業新聞社様発行「工場管理」https://pub.nikkan.co.jp/search/g103352.html)
このたび、弊社製品が5月号に掲載されますので、4月18日発売予定の「工場管理」5月号、「モノづくりにおける異物対策」にご興味のある方は、ぜひお買い求めください。
なお、先着10名様に弊社から「工場管理2025年5月号」をプレゼントさせていただく予定です。(2025/4/18以降)
i-PROWは、中小製造業者様にとって、不良率をおさえるためのトラブル管理を強力にサポートするツールですので、ぜひデモ体験のお申込み・資料請求をお待ちしております。
雑誌「工場管理」5月号プレゼントも以下のフォームからご応募ください。(2025年3月25日現在。先着10名様まで。人数に達し次第締め切り。)